Norbert Brandau can see the construction site fence from his desk. When we meet him for our interview, he is wearing his yellow high-visibility jacket, which is part of his everyday work outfit. The fence in his office, however, is only temporary. Soon there will be offices for the employees of the new Amazon fulfillment center HAM 2 in the town of Winsen (Luhe). Like all other Amazon sites, HAM 2 is named after the closest airport, located in Hamburg Fuhlsbüttel. The fulfillment center started operations end of July and is planning to run at 100% in December.
We started in HAM 2 in July and are planning to run at 100% in December.
Norbert Brandau is the site manager and responsible for staying on schedule. During the setup of HAM 2 one of his main tasks is hiring new employees, 150 per week in August alone. The big goal is setting up the Fulfilment Center as soon as possible for storing products and for preparing shipments to the customer. For that, he has to make sure that the new team and also new technology will soon be ready to go. "Everyday there are new challenges and new mistakes that we are learning from," explains Norbert Brandau. It is of particular importance to him to find the strengths of new employees to know in which area they could work best.
When moving into a new building, there is no set standard for how to set up a workstation. The workers at the packaging-line had to re-assemble their workstations ten times - all within two days. Those are the moments where Norbert Brandau has to improvise.
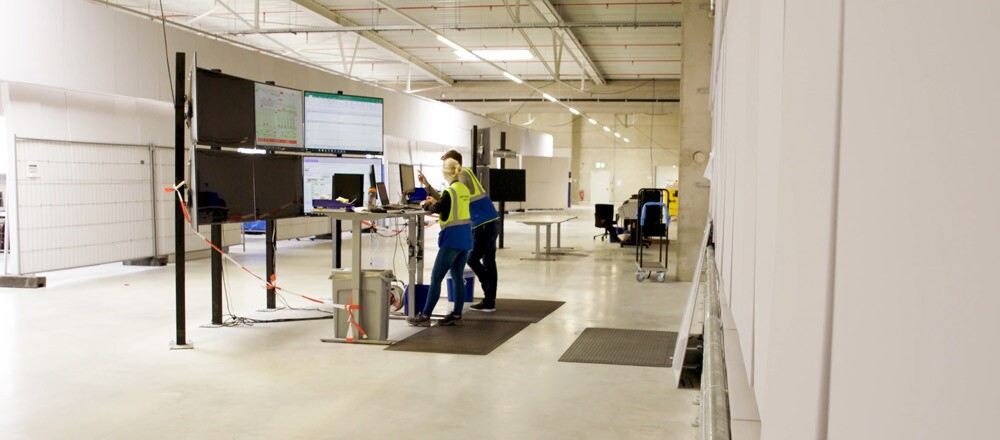
While people in the corridor next to Brandau's office are still unwrapping office chairs, he already has the next challenge in mind: "HAM 2 is the first fulfillment center in Germany that uses Amazon's robotics technology," he said.
HAM 2 uses transportation robots - the so called "Drives".
This new technology is mostly used for storing and picking products in the warehouse. The compact, orange robots are real powerhouses. They can move independently from A to B to C around a big, closed off space in the storage area. They drive under the shelves, lift them up or lower them and bring the stored products directly to the workers at the packaging line. Area manager Alexander AI Rayes is fascinated by how much storage space the Drives save. The shelving and storing system is optimized for the nimble Drives, which can rotate 90 degrees on the spot while they are each transporting a shelf. Stickers on the floor tell the Drives exactly where they are at all times so they can easily pass by each other.
"The Drives contribute to a very positive work environment. One of the main advantages is that we barely have to walk around the warehouse anymore. That makes our workspace more comfortable and safer," said Alexander AI Rayes.
Every day brings a new challenge.
Monika knows these types of situations. She started eight years ago as a seasonal worker in the receiving area and worked her way up to becoming an operations manager. Now Monika is using her experience to ensure stable processes in HAM 2. "The first few months, where everything is coming together, are very special. That's when the team spirit is getting built. These experiences are something everyone will tell their future co-workers about some day," says Monika. Looking ahead she said: "I am looking most forward to not having any more construction noise in our facility and nobody will have to wear a helmet".