At Amazon, our delivery stations may be the smallest buildings in our operations network, but they play a crucial role in ensuring our customers receive their orders on time and in good condition. Every day, these facilities run roughly 40 operational processes to prepare thousands of packages for delivery to customers in nearby communities. Employees receive the packages, sort them to the final delivery route, pack them into bags and prepare those bags to be picked up by our delivery service partners. To make these jobs safer and easier, we expect to have invested more than €700 million in technology innovations across our European delivery station network from 2021 till the end of 2025.
Why now?
As we look to the future, we want to ensure that we create more high-skilled work that is ergonomically sound for young and aging populations alike. Technology is helping us achieve this vision.
In recent years, we’ve been automating physical, repetitive tasks in our fulfilment centers, building the world's largest fleet of 750,000 industrial robots that collaborate with our employees. Our growing scale and expanding use cases have helped drive down technology costs, allowing us to implement robotics and automation across other parts of our operations, like our package delivery network.
Transforming delivery stations with technology
When we began delivering packages to customers in Europe in 2012, most operational processes in our delivery stations were manual, with limited technological support. Since then, we've been developing, testing, and implementing innovations that create better, safer work environments while enabling faster delivery.
We opened the Last Mile Innovation Center in Dortmund, Germany, that serves as a globally unique testing facility where we develop the technologies that will shape the next decade of our delivery business. Here we have successfully tested the concept of the “delivery station of the future” and we expect the first fully operational delivery station in line with this concept to launch in 2026 in Europe.
Here are some of the innovative technologies that will support employees and handle the most repetitive, physical tasks:
Tipper
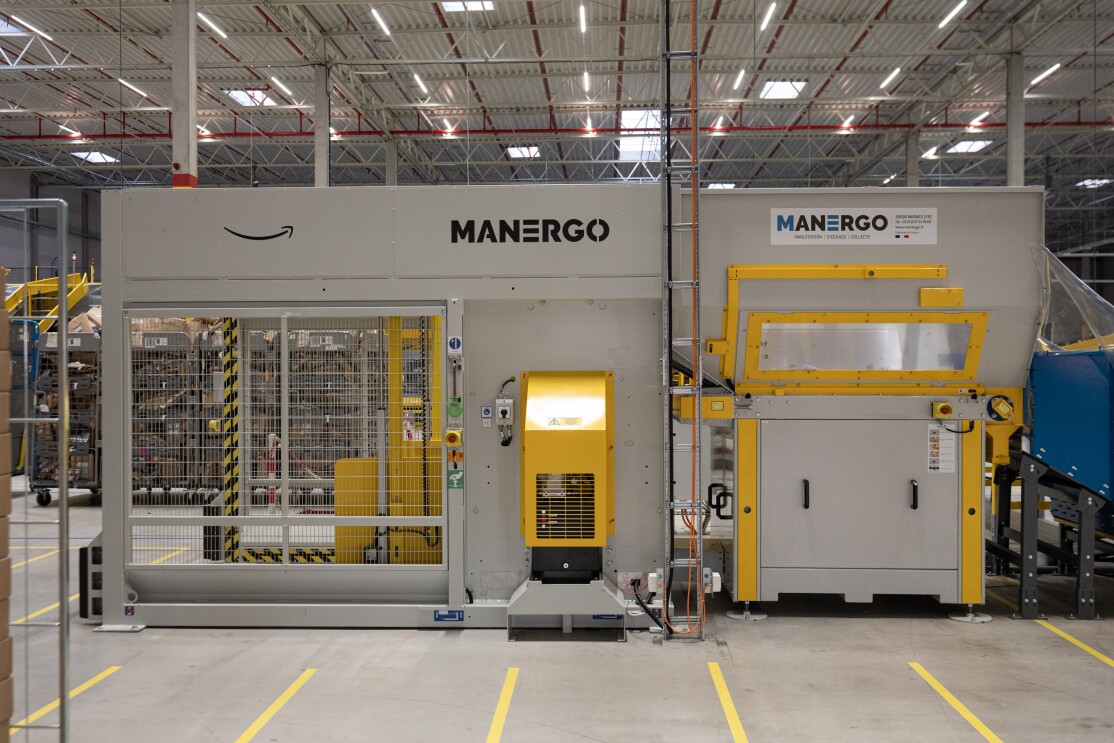
An automated solution that eliminates the need for manual package unloading. Instead of physically removing packages from carts, employees simply bring carts to this innovative system, which automatically transfers packages onto the conveyor belt. This technology significantly reduces physical strain while maintaining efficient package flow.
Echelon and six-sided scanner
These two complementary technologies are working in perfect harmony. The Echelon system manages package flow on conveyor belts, while the six-sided scanner automatically captures package information from every angle. Together, these innovations eliminate the need for manual scanning and handling, creating a more streamlined process.
Agility and Matrix
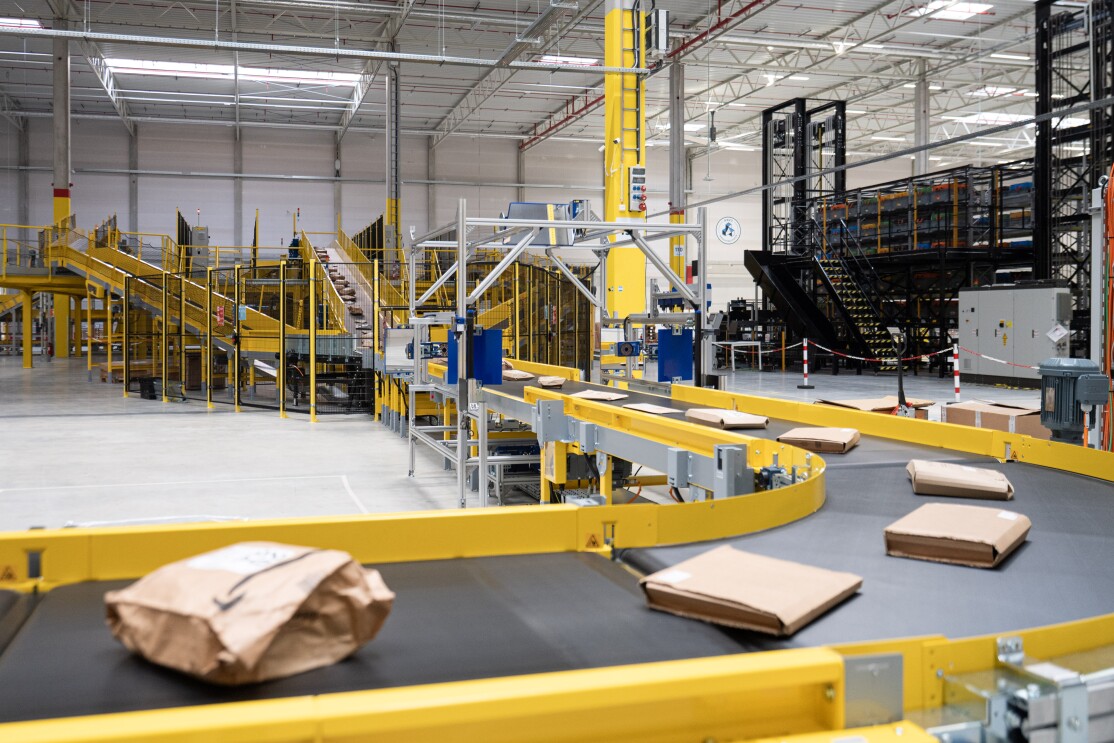
These sophisticated technologies determine optimal paths for package sorting. They minimize the need for employees to push, reach for, or manually handle packages, creating a more efficient and ergonomic work environment.
ZancaSort
A transformative technology that brings packages and their designated bags directly to employees at an ergonomic height. With this tech in place, employees no longer need to walk through numerous aisles or reach to stack parcels. They simply place packages into their designated bags, making the process more efficient and significantly more comfortable.
Vision Assisted Sort Station (VASS)
This innovation uses computer vision and projection technology to help employees sort packages more efficiently. It visually highlights packages and their correct sorting locations, making it much easier for employees to quickly match thousands of packages to the right delivery route bags.
Creating new opportunities
These innovations don’t mean we’ve slowed on hiring. Since introducing robots within Amazon’s operations, we’ve hired hundreds of thousands of employees to work in our facilities. And we continue to invest in skills-training programs, as instead of someone performing manual tasks sorting packages, that person can be trained to operate the technology that provides support.
In 2024 alone more than 20,000 employees in our European delivery station network acquired new skills related to operating automation technology and AI-powered innovations. In addition to that our employees can chose to develop certain skills. Our Career Choice skills-training program pre-pays funding for nationally-recognized courses to support current and future job needs for thousands of employees. Our data shows that close to 30% of active Career Choice participants in Europe are enrolled in technology upskilling courses and it is the most popular pathway amongst our employees.
Deployment of technology also means that we need people to design it, create its software, control and maintain it. In the past two years, we increased the number of delivery station employees in reliability, maintenance, and engineering roles in Europe by more than 50%.
I'm incredibly proud of the progress our teams have made since launching our last-mile network in Europe in 2012. We remain committed to investing in technology that creates better, safer jobs and speeds up customer deliveries.